Coatings Technology Blog
Engineered Coatings For Corrosive Oil And Gas Applications
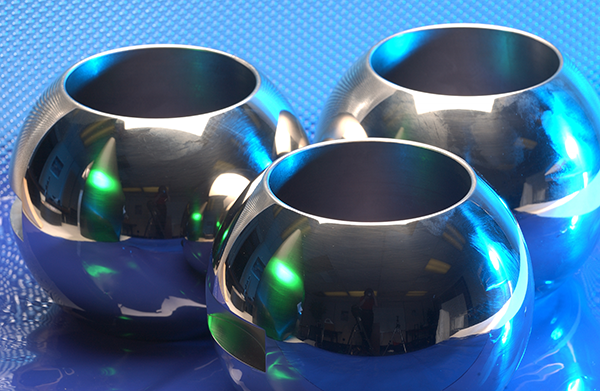
For increasingly corrosive conditions in oil and gas applications, standard coating technologies can marginally protect drilling tools against harmful galling, corrosion, pitting and other wear mechanisms that trouble drill strings. Engineered coatings, however, do an even better job protecting these tools from the tough conditions in deep wells.
In this post, we’ll examine some traditional coating problems in oil and gas applications, and tell you how our engineered coatings do a better job solving them than generic coatings.
Traditional Coating Problems. Many types of coatings work adequately when used in the proper application. Standard or traditional coatings such as hard chrome, QPQ, fluoropolymers and tungsten carbides have long been used in oil and gas applications with some success.
The problem is that these traditional coatings don’t stand up to the levels of sour gas, pressure and rotating contact found in today’s oil and gas wells. Some designers still employ a nitride process or quench polish quench (QPQ) to reduce coefficient of friction and increase tool life, but these treatments case harden the part. QPQ penetrates six to ten thousandths into the part, changing its metallurgy. Tools used to spin, grab or lift QPQ treated components have shown limited ability to grip the case hardened components as they essentially are too hard for the tool to bite into.
Engineered Coatings. New engineered coatings are a much better choice for oil and gas applications than these traditional technologies. Take hardness, for example. A Nedox® synergistic coating with a coefficient of friction comparable to a 2H-hardness fluoropolymer coating ‘ups the ante’ on hardness to 68 Rc.
The major advantage of engineered coatings versus other types, such as paint-on varieties, is that the particles in synergistic coatings become an integral part of the substrate. Engineered coatings are mechanically bonded to the metal and the resulting new surface layer resists chipping, flaking, peeling or rubbing off. Because these coatings create metal surfaces that offer superior performance to both the original base metal and conventional coatings, these surface enhancements are said to be synergistic.
Further, because the engineered surfaces either duplicate or surpass the performance characteristics traditionally provided by metals such as chromium, cobalt, cadmium, and manganese, use of these expensive materials can be reduced.
System Design Advantages. Engineered coatings can improve drill string components as well as gate valves, impellers, rotors and mud pump components. They reduce friction and wear, and provide protection against corrosion and chemicals. Synergistic coatings such as Plasmadize®, Nedox and Magnaplate HMF® allow tool designers to make the drilling operation and extraction more efficient by downsizing casings and making components smaller. Initial tool costs can be lowered by employing reduced amounts of tooling material and less expensive metals.
Longer term, the improved COF and chemical resistance of surface enhanced parts increases the working life of tool and minimizes down time. System design advantages, such as power reduction, can also be realized with decreased COF and smaller, lighter tools available with engineered surface enhancements.
For more details, download our white paper.