Coatings Technology Blog
The Benefits Of Magnesium Coatings In Aerospace Applications
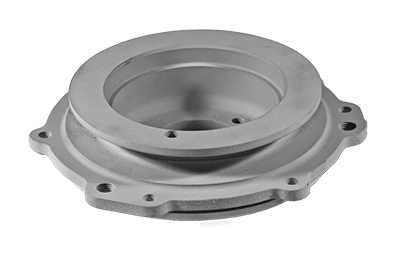
Magnesium alloys, which are gaining popularity in the aerospace industry, must be able to withstand very harsh conditions. The right surface enhancement coating can help. In addition to handling thermal extremes, preventing outgassing and minimizing friction, your magnesium coating should come from a AS9100:D-certified supplier—ensuring it’s passed stringent quality requirements for use in demanding aerospace applications.
An example of a coating that fits the bill is MAGNADIZE®, which provides superior protection for magnesium parts. Let’s take a closer look at what this coating brings to the table:
MAGNADIZE® Prevents Wear, Outgassing And More
Magnesium alloys are popular thanks to their high strength-to-weight ratio, dimensional stability and low density, which is roughly one-quarter that of steel and two-thirds that of aluminum. As a result of these properties, these alloys can drastically reduce the weight of aircraft, which in turn reduces fuel consumption and CO2 emissions. At the same time, lighter magnesium alloys are more susceptible to corrosion, galling and wear if left uncoated.
MAGNADIZE® overcomes these challenges. This proprietary coating—which meets Mil-M-45202 requirements—uses supplementary polymers or dry film lubricants to protect against wear and prevent outgassing. It also surpasses other current methods of magnesium treatment, such as magnesium anodizing or HAE anodizing, when it comes to preventing oxidation. Other technical advantages of MAGNADIZE® include:
Wide operating temperature range. Aerospace components have to endure high heat and extreme cold. MAGNADIZE® features a wide operating temperature range of -100° to +550°F—ensuring surface protection in the harsh vacuum and low temperatures of outer space.
Low coefficients of friction. One way to reduce friction is to apply grease or oil to components. This method, however, requires routine maintenance and can release harmful particulates into the atmosphere. MAGNADIZE® offers an eco-friendly, permanent solution that boasts coefficients of friction as low as 0.05.
Galling prevention. Metal galling, caused by adhesion between sliding metal surfaces, is a common industry challenge that causes parts to self-generate an oxide surface film. MAGNADIZE® avoids this form of wear by creating hard, fracture-free surfaces that prevent hydrogen absorption from occurring between the metals.
The Advantages of ISO 9001:2015 and AS9100:D Certification
Significantly, Magnaplate is ISO 9001:2015 and AS9100:D-certified. These certifications ensure the competency, capability and consistency of our manufacturing processes and ensures our coatings, include MAGNADIZE®, meet the highest possible quality standards for use in aerospace.
To learn more about MAGNADIZE®, visit our coatings page.