Coatings Technology Blog
Surface Enhancement for Metal Parts - Advantages of Electroless Nickel Plating
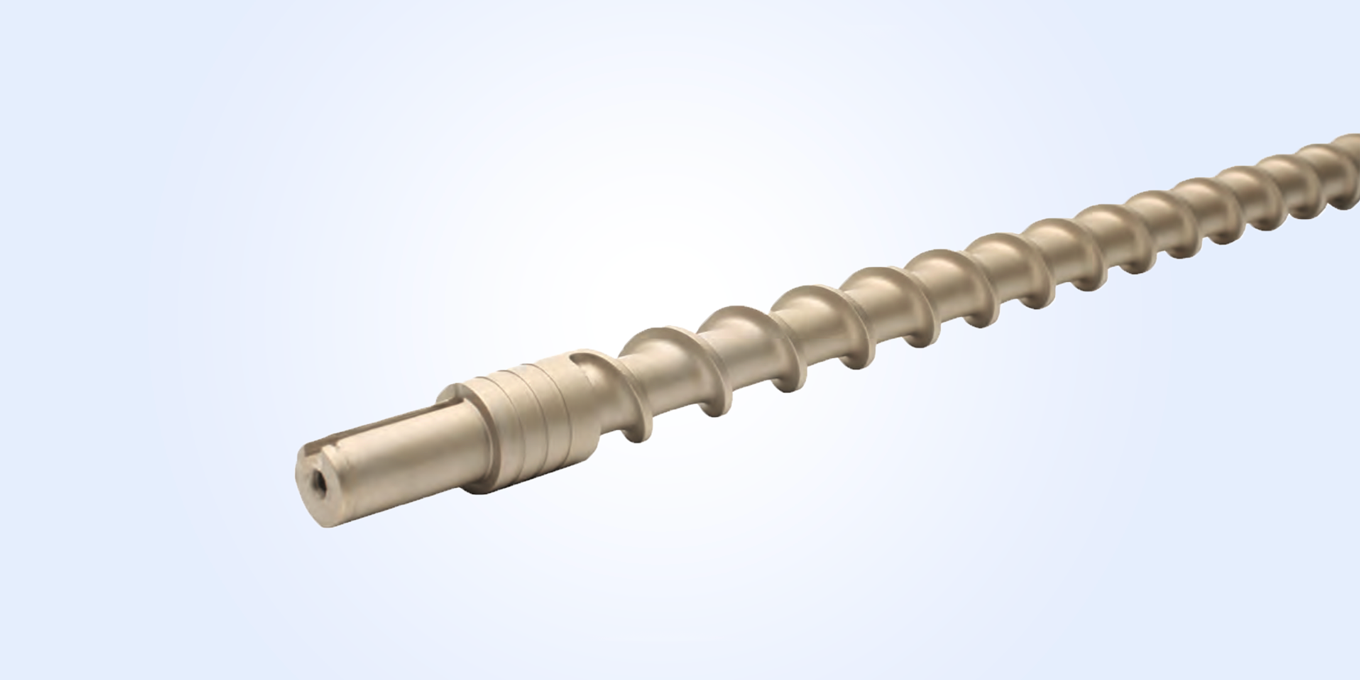
Selecting a coating to protect and enhance your metal part can be a difficult process. While there are many surface protection options to evaluate, electroless nickel boasts several benefits that make it desirable for certain requirements. Here’s a brief exploration of the distinct advantages that electroless nickel plating can offer versus alternative processes.
Electroless Nickel Process Advantages Versus Alternative Coating ProcessesElectroless nickel plating offers excellent protection against wear, friction and corrosion. This autocatalytic process does not require an electrical current, external power or complex anodes. It produces a uniform coating even on sharp edges and corners that otherwise cause high current density buildup with electrolytic processes. Besides its versatility, electroless nickel offers additional advantages versus alternative processes:
- Consistency. Because electroless plating is an immersion process, it applies a uniform coating to any surface it can access. It typically does not require secondary machining and finishing steps, is unaffected by line of sight and can even travel into blind holes.
- Outstanding surface hardness. Nickel can carry a high Rockwell Hardness value. In fact, certain electroless nickel plating processes boast hardnesses that are comparable to hard chrome when heat treated — without a degradation of fatigue strength or the possibility of galling or seizing.
- Tight tolerances. Coating uniformity allows electroless nickel to achieve tighter tolerances. For instance, thermal spray coatings can only hold a ±0.002-inch tolerance, whereas electroless nickel can hold a ±0.0002-inch tolerance, as applied, and sometimes tighter.
Higher-Performance Nickel-Based Coating Option Provides Optimal Metal Parts Protection
While electroless nickel plating offers undeniable benefits, there is a higher-grade nickel-based coating option available for applications that demand maximum protection and performance. Magnaplate’s Nedox® family of surface enhancement coatings contains polymers and dry lubricants to give the base metal optimal durability. This synergistic coating creates a harder-than-steel, self-lubricating surface that protects against wear, corrosion, sticking, galling and static buildup. It provides superior mold release and is permanently dry-lubricated to produce a low coefficient of friction that eliminates stick-slip and undesirable vibration. Magnaplate can also assist customers to create a special chemistry, phosphorus concentration or heat treatment to solve specific problems. Nedox features include:
- Resistance to corrosion, chemicals and acid.
- Meets ASTM B733 requirements plus many FDA and USDA codes.
- A wide operating temperature range: -250°F (-157°C) up to 1,500°F (816°C).
- Surface hardness to Rc 68.
- Coating thickness between 0.0002 to 0.002 inches.
- Typical coefficient of thermal expansion: 7.22 x 10–6 in/in/1°F. (13 x 10–6 in/in/1°C).
- Typical coefficient of thermal conductivity: .0105 to .0135 Cal-cm/sec/°C.
Magnaplate backs up its high-performance process with a host of quality control measures such as monthly corrosion, salt fog and hardness tests as well as coefficient of friction tests, eddy current readings and adhesion inspections. The company maintains strict bath records, and auto-feed systems keep chemistries in balance. The result demonstrates quality to ISO 9001-2015 standards as well as AS9100:D certification – the aerospace industry’s strict accreditation for special processes.
Protecting metal parts can be a daunting challenge thanks to the many different coatings engineers must choose from. Magnaplate’s Nedox synergistic surface enhancement coatings protect most metals while delivering superior performance.