Coatings Technology Blog
To Keep Mining Operations Running, Protect Valves With Engineered Coatings
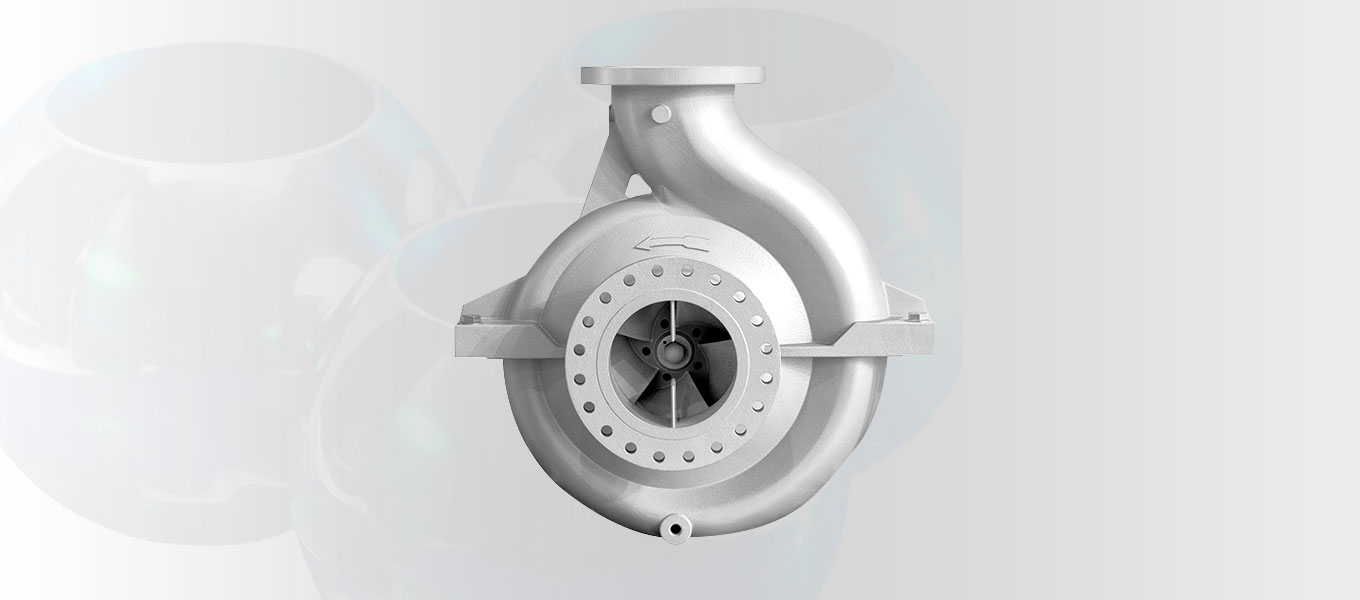
Mining and mineral processing facilities present a host of threats that can affect valve reliability and uptime. Knife gate valves used in slurry transport, for example, must consistently perform despite heavy contact with abrasive, corrosive metal solids or acids that can erode the valve. Slurry materials and sludges can also stick to valve parts, impeding flow. If your valve fails or leaks, consequences can include replacement, downtime for repairs, environmental damage and safety risks to personnel.
Avoid Damaging Corrosion, Wear and Buildup
Magnaplate coatings have proven successful protecting valves from the damaging effects of mining operations. Our coatings are specially engineered to provide wear, friction and corrosion resistance — three properties critical to the protection of mining valve blades, housings and other vital parts. Engineered coatings transform ordinary metal parts into corrosion-resistant, super-hard, dry-lubricated products that last longer, are more cost efficient and perform better.
Engineered coatings offer mining valves these and other benefits:
- They can perform in low or high pH conditions, providing excellent resistance to both acidic and caustic threats.
- Many coatings are suitable for use in high temperatures up to 850°F (454°C).
- Exceptional hardness: Engineered coatings can exhibit hardness as high as 68 Rc or beyond.
- Consistent quality: Thickness tolerances as low as ±0.0002 inches.
The result: Less downtime, easier preventive maintenance and improved productivity. That’s why Magnaplate coatings protect valves in coal-fired power plants, wastewater treatment, green liquor isolation, sand removal cyclones and high pressure booster pump stations. Here are some examples of engineered coatings as they correspond to corrosion, wear and sticking:
- For corrosion resistance:
- Lectrofluor®. This proprietary polymer-based coating family was developed to prevent severe corrosion and chemical attack in hostile environments. They also offer high oxidative stability, excellent mechanical toughness and cut-through resistance.
- Magnaplate HCR® exhibits extraordinarily greater corrosion resistance than common industry processes, and it withstands salt spray exposure on aluminum in excess of 15,000 hours — 44 times the MIL-SPEC of 336 hours.
- For protection against wear:
- Nedox® provides superior protection against wear, friction and corrosion. Additional features include hardness up to Rc 68 and excellent lubricity.
- Plasmadize®. These thermal spray composite coatings resist abrasion and corrosion, and they extend wear life with hardness beyond the Rc scale. Some types offer a low coefficient of friction, making them especially suitable for use with sliding objects.
- For release from sticking:
- Nedox is also well-known for preventing sticking, which can otherwise cause sludge to accumulate. In fact, Nedox helps valves open and close smoothly without damaging the valve’s packing materials, thereby minimizing buildup and making cleanup easier.
- For associated equipment:
- Magnagold® protects tools and drill bits.
Because mining applications present a variety of challenges to valves, Magnaplate engineers can review your application details such as the slurry materials and pH ranges your valve will encounter. They’ll review the available coatings and their characteristics so the best one can be selected for the job.
Engineered Coatings Optimize Flow and Maximize Uptime
Mining valves must operate dependably despite constant exposure to harsh conditions. Magnaplate coatings are engineered for demanding applications so you can be sure they’ll stand up to corrosion, abrasion and wear when you apply them to your valves. That means optimal flow of media and maximum uptime for your mining operations.
Learn more about Magnaplate engineered coatings.