Coatings Technology Blog
Engineered Coatings Protect Valves in Harsh Conditions of Oil and Gas Facilities
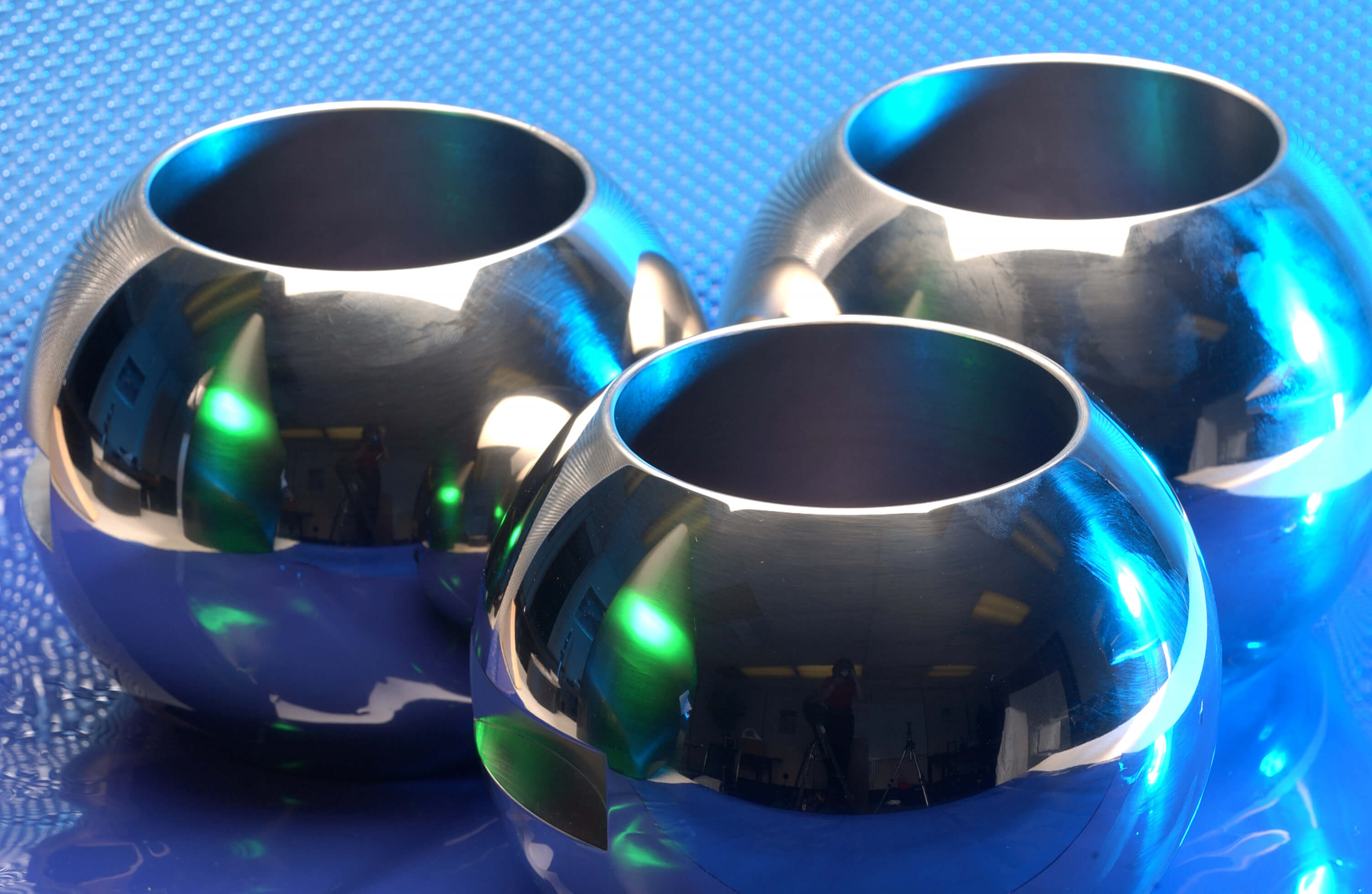
As oil and gas facilities move to more remote locations with extreme conditions, any equipment downtime due to parts failure can be costly. Valves must perform reliably despite exposure to corrosive chemicals, abrasive fracking fluids, sour gases in drilling, high pressures, liquids, variable pH levels and high temperatures. In addition, contact with other metal tools can cause galling which can result in premature wear, leaking and ultimately valve failure. Many types of coatings can offer basic protection. But when your valve has to withstand this type of punishment, you need the peace of mind that comes from engineered coatings.
Magnaplate engineered coatings stand up to abrasion, galling and corrosion that threaten the performance of ball valves, gate valves, globe valves, safety valves, pressure valves and tools. Unlike other coating options, Magnaplate coatings can be modified to meet an application’s specific functional criteria based on the intended environment. In fact, the coatings become an integral part of the substrate, so metal surfaces like aluminum become super hard. The result: long-lasting parts plus performance characteristics that can even surpass more expensive metals. Many engineered coatings are suitable for use in low pH conditions in which corrosion is a concern as well as in high temperatures commonly found in the oil and gas industry.
Coatings Stand Up to Galling, Abrasion and Corrosion
When you need a protective coating that stands up to unforgiving oil and gas conditions, certain engineered coatings come to mind:
- Nedox®. Suitable for all types of metal parts, including valves and others made of aluminum, Nedox creates a harder-than-steel, self-lubricating surface that resists corrosion, friction, sticking, galling and static buildup. It is also highly resistant to salt spray. Suggested Nedox use cases include:
- For abrasion resistance: CR+, SF2 and PFF.
- For galling resistance: CR+ and SF2.
- For corrosion resistance: SF2, CR+, 10K3.
- Magnaplate 10K3™ replaces conventional coatings that can't endure temperatures above 500°F, and it can be applied to all Magnaplate coating families. Benefits include good release properties and excellent corrosion resistance up to 850°F.
- Magnaplate HMF®. Engineered from a proprietary, multi-step coating process, this coating produces a mirror-smooth surface with a microfinish as low as 4 Ra that can produce a low coefficient of friction. Magnaplate HMF can obtain a hardness of up to 68 Rc, resists moisture and prevents galling and seizing.
- Lectrofluor®. This proprietary polymer-based coating family offers good release properties and resists corrosion and wear.
Two engineered coatings — Nedox 10K3, and Nedox CR+ — were tested to NACE 0284 test specifications for hydrogen-induced cracking in sour environments and passed after 96 hours of exposure. Magnaplate maintains strict quality control through automated processes along with regimented monitoring and cleaning processes at its ISO9001 accredited and AS9100-certified facility, so customers can be sure their valves and parts are always protected. Keep in mind that Magnaplate can customize your coating selection within a family.
How to Get the Right Engineered Coating for the Job
As you consider engineered coatings to protect valves for your oil and gas equipment, be sure to consult Magnaplate early in the selection process and, when possible, pre-size the parts to account for the potential coating thickness tolerance. Design engineers should also consider their base metal preferences, desired tolerances and environmental factors such as the pH conditions, potential exposure to abrasives and cleaning processes. We’ll then suggest the most relevant engineered coating for your oil and gas application.
Valves used in unforgiving oil and gas reservoirs and refineries require the highest quality protective coatings. Magnaplate produces engineered coatings that exhibit the hardness and consistent quality that oil and gas applications require to give you long-lasting protection against abrasion, galling and corrosion.
For more information about Magnaplate engineered coatings for valves used in oil and gas facilities, visit the industry page.