Coatings Technology Blog
Engineered Coating Unsticks Food Processing Operation
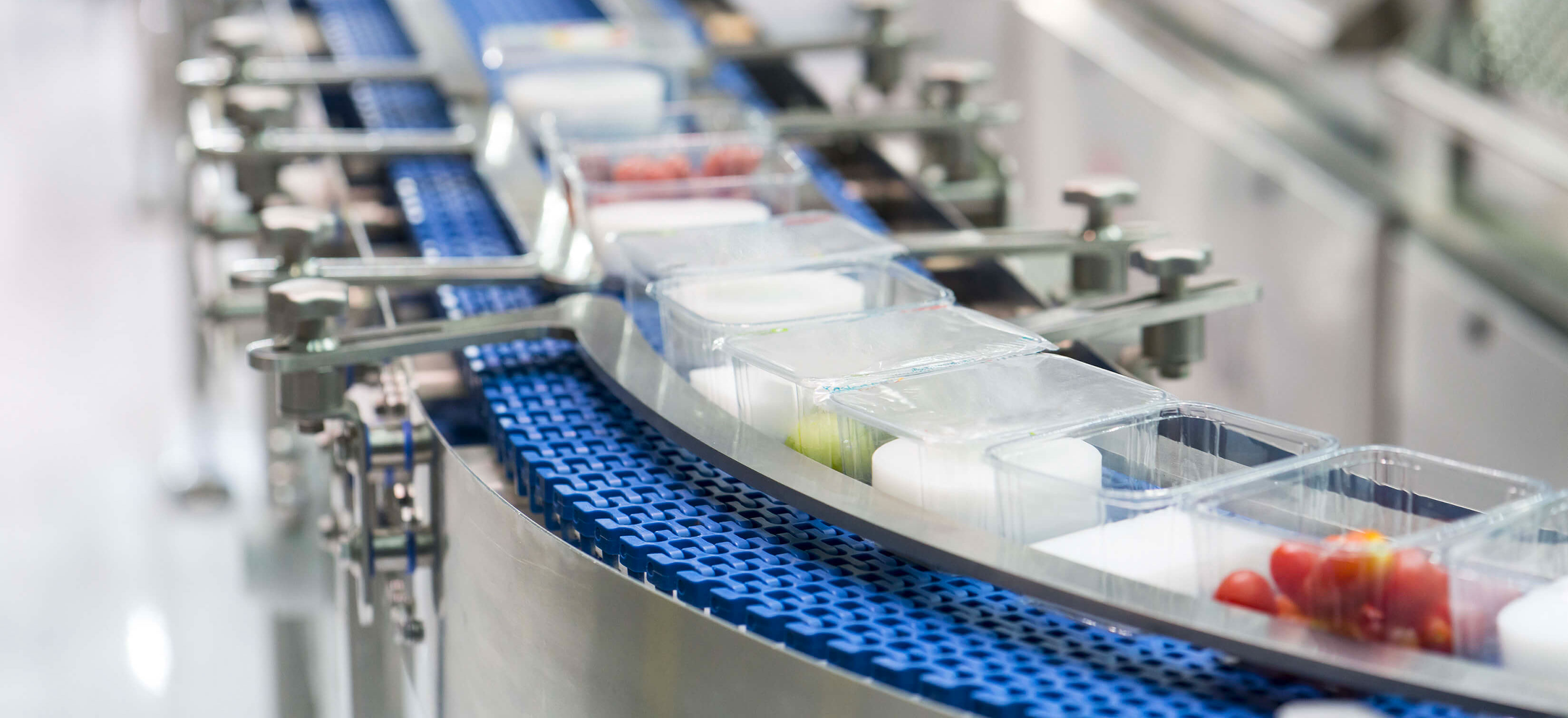
Sticky glues and adhesives as well as wear and abrasion are particularly common threats to machine reliability, and they can halt production as workers clean and repair the damage. Over time, these interruptions can significantly impact the bottom line. That’s why a large food processor recently began working with us to help solve a nagging source of downtime and machine repair.
This food processor had a longstanding problem with a lunch meat product that gets placed in a molded plastic tray and heat-sealed inside a clear film. When employees sealed the product, mistakes often caused the film to stick to the sealing plates. Not only did the company lose approximately 30 minutes of production time to remove the film from the plates, the employees had to remove the film using picks and scrapers that ultimately damaged the plates. For an operation that molds several thousands of plastic trays per day, time and money lost to cleaning and repair substantially impacts the bottom line.
The production manager made corrections to the manual sealing process and chose a PTFE coating for the sealing plates. The PTFE product alleviated the issues caused by botched manual sealing, but it fell short once the process was corrected and improved. The coating was not engineered to match the application’s needs when the process is done properly.
However, a Magnaplate Nedox® surface enhancement coating had proven successful for a similar product in another part of the company, so the manager explored transitioning the heat seal plates from the PTFE coating to Nedox as a solution. In addition to being impressed by the previous application, the production manager also liked Nedox’s sleek, lubricious finish. This USDA- and FDA-compliant coating family also features good performance in chemically corrosive environments subject to washdown conditions, and it helps make machine cleanup easy.
Nedox was applied to two different seal plates — a three-cavity and a four-cavity plate. The application has two main objectives: eliminate wear and abrasion from occurring on the heat sealing plates and provide good release of sticking from the sealing residues. And this heat sealing plate application has no margin for error: Because the sealing surfaces are extremely critical, any chips, dings or defects in the coating can cause these parts to be rejected.
After a successful transition, the food processing customer is very happy with Nedox’s performance. The deposition process went smoothly with no ill-effects to the heat plate surfaces. The company reports that the release is no longer an issue, and the coating is providing excellent wear resistance. As a result, the sealing machines are running longer and using less parts while downtime for cleaning has been greatly reduced. And all these performance benefits have delivered significant cost savings.
Proprietary, Engineered Coatings Provide Better Value
When it comes to food and packaging applications, wear, abrasion and sticking are among the main causes of expensive machine downtime and lost productivity. While various standard and lower-cost coatings can help protect against these threats, Magnaplate’s proprietary coatings like Nedox are engineered to match specific application needs. Using Nedox, the lunch meat product manufacturer is able to keep machines running without worrying about wear and sticking issues that previously slowed down the operation, achieving a greater value that comes from time and cost savings.