Coatings Technology Blog
Understanding the Many Facets of Corrosion
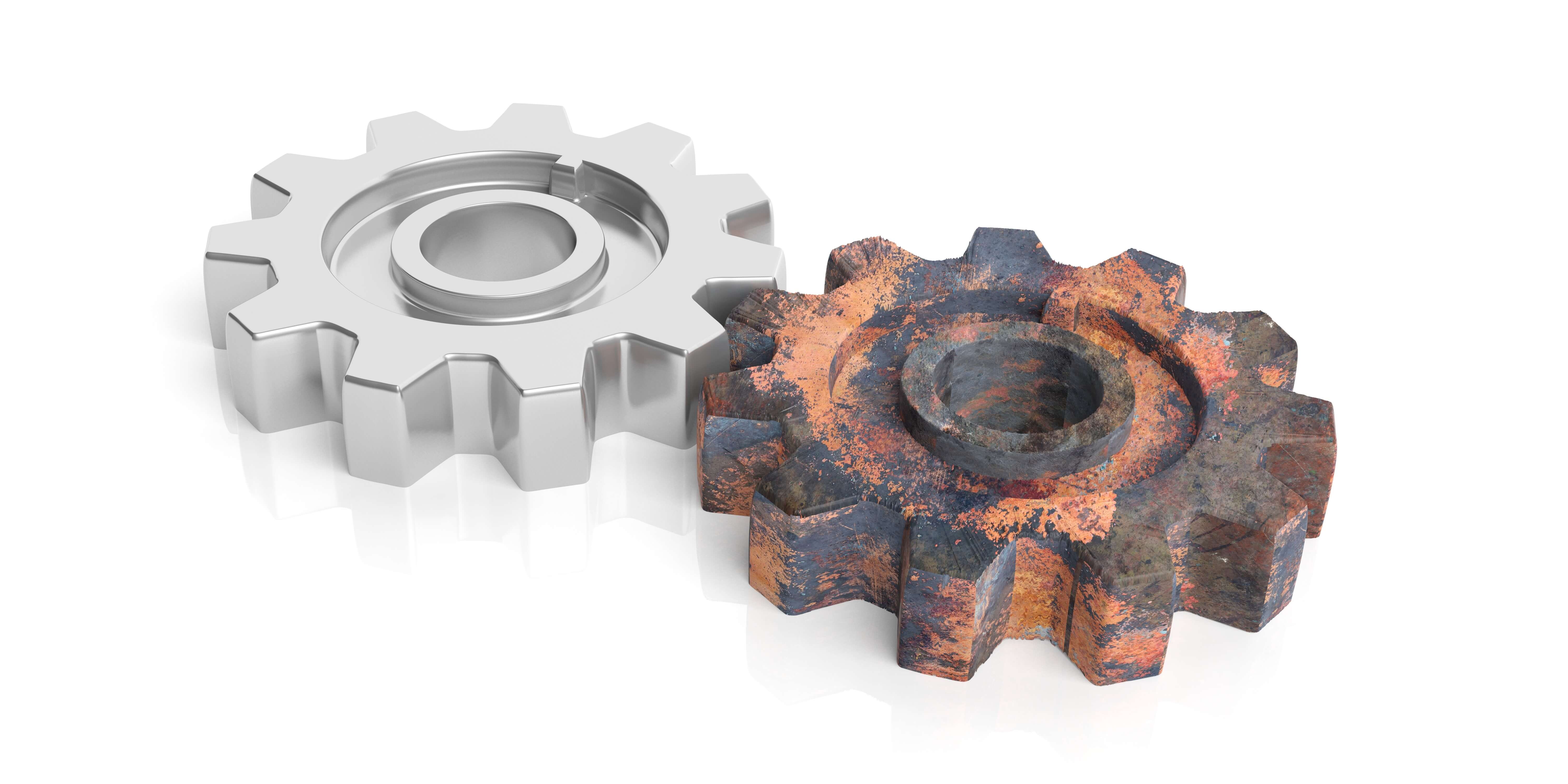
Sometime during your metal or alloy part’s lifetime, it will be vulnerable to corrosion. Corrosion is a common problem, and it occurs in many different forms. If you’re trying to protect a metal part, chances are a simple solution will not be sufficient. In order to address the problem, it pays to have a good understanding of corrosion and its effects.
Corrosion is a natural process that converts a refined metal into a more chemically stable form via chemical or electrochemical reaction with the environment. The reaction requires a metal to serve as an anode where electron loss occurs, and a cathode for reduction, or electron gain. The anode and cathode are electrically connected, and a voltage difference will exist between them.
The process can spread uniformly across an entire surface or occur locally in a particular area. Here are the common types of corrosion that can cause problems for your part:
- Galvanic corrosion is a coupling of two dissimilar materials in a corrosive electrolyte such as water. One of the metals in the couple becomes the anode and corrodes faster than it otherwise would on its own, and the other metal becomes the cathode and corrodes more slowly.
- Crevice corrosion results from concentration differences of ions or dissolved gases in the electrolyte when a stagnant environment exists under objects like gaskets, washers and fastener heads or other materials at their point of contact with the surface.
- Pitting is a localized form of micro-structure corrosion that produces holes or pits of different shapes in the material. It is difficult to detect, predict and design against.
- Intergranular corrosion, another localized micro-structure corrosion type, occurs along and near grain boundaries that separate metals and their alloys. Anodes can easily form at the boundaries as galvanic cells or a concentration of cells. The anodes have a very small area, which may allow a rapid spread of corrosion.
- Corrosion-assisted fatigue happens when corrosion causes pits, trenches and other stress concentrators to amplify the stress level in affected regions.
- Stress corrosion cracking results when tensile stress is applied to a component in a corrosive environment. This leads to anode formulation at the affected sites. Once a crack starts, stress concentrations intensify and accelerate the cracking.
Common Corrosion Prevention Methods
Methods to protect surfaces from corrosion are designed to interfere with the reaction that forms the electrochemical cell.
- Anodic protection. Makes the metal surface the anode and controls the electrode potential in a zone where the metal is passive.
- Cathodic protection. Makes the metal surface the cathode and transfers the corrosion from the protected surface to a more easily corroded “sacrificial” metal.
- Encapsulation. Coating a surface to prevent exposure to corrosive elements.
Most Magnaplate coatings impart corrosion protection to metal surfaces. Because corrosion takes so many forms, many variables need to be taken into account when choosing a coating. That’s why our coatings are “engineered” for specific factors of an application that demand special attention to stop corrosion. When you work with us early in the design process, our experts can discuss coating options and modifications that can help you meet your corrosion protection requirements.
Look Beyond a One-Size-Fits-All Approach
Because corrosion can occur in a variety of ways, engineers should not take a one-size-fits-all approach to mitigate the problem. Magnaplate’s experts can work with you to tailor a coating with the characteristics you need so your part can perform reliably wherever corrosion is a threat.
For more information about how Magnaplate engineered coatings can address corrosion, contact us.