Coatings Technology Blog
Inside Magnaplate’s Culture of Continuous Improvement
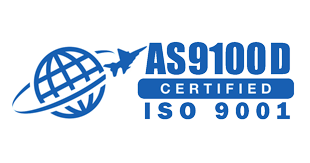
When you learn that a company has earned AS9100 certification, you know it is committed to continuously improving its operations. Carrying out the policies and procedures required to achieve and maintain the certification requires company-wide participation and coordination. For example, in recent years the AS9100 standard has included safety objectives, addressing counterfeit parts and approaches to risk-based thinking. These initiatives involve multiple departments and multiple stakeholders.
Magnaplate has an entire department of professionals that conduct internal audits to make sure that the parts leaving our facility meet customer requirements and expectations. For example, the Quality Control department includes an Internal Audit Manager who maintains the company’s AS9100 quality management system by performing internal auditing, analyzing quality metrics and providing support for quality investigations. The Quality Control department has two objectives: acting as a barometer to identify production areas demanding specific attention, and providing an early warning system by harnessing customer feedback and our quality information system to go straight to the source of the problem and offer help to fix it.
Internal audits measure the effectiveness of our quality management system and identify areas that need improvement. They are a great learning experience for both the auditor and the auditee. Auditing can provide great insight into weaknesses and strengths within our process that may not be obviously visible.
How Does Our Quality Control Department Affect the Parts That You Receive?
The Quality Control department maintains critical programs that can directly affect part quality and customers' expectations. One great example is our calibration program, which guarantees that instrumentation used in processes and final inspection is accurate. Failure to maintain a strong calibration system could result in unknowingly shipping poor-quality parts to customers. Another important function? Maintaining up-to-date process specifications. The Internal Audit Manager acts as an intermediary between the lab and production departments. By communicating with each department, the manager gains a good understanding of processes which provides greater opportunity to identify and offer improvements as well as overcome existing challenges. We regularly interact with our customers and learn their quality requirements in order to understand their needs and ensure they are integrated into our processes.
Our Dedication and Commitment to Quality and Safety
The AS9100D certification standard was originally developed for the aerospace industry to ensure the highest levels of quality and safety. Our constant internal audits, comprehensive documentation, ongoing training and company-wide adherence to correct procedures are all integral to delivering your part, to your requirements, with the highest quality. It wouldn’t be possible without the dedication and commitment of all our associates along with the guidance of our Quality Control department.
For more information about Magnaplate, contact us.