Coatings Technology Blog
Tufram® Takes the Heat in Aluminum Heat-Sealing Equipment
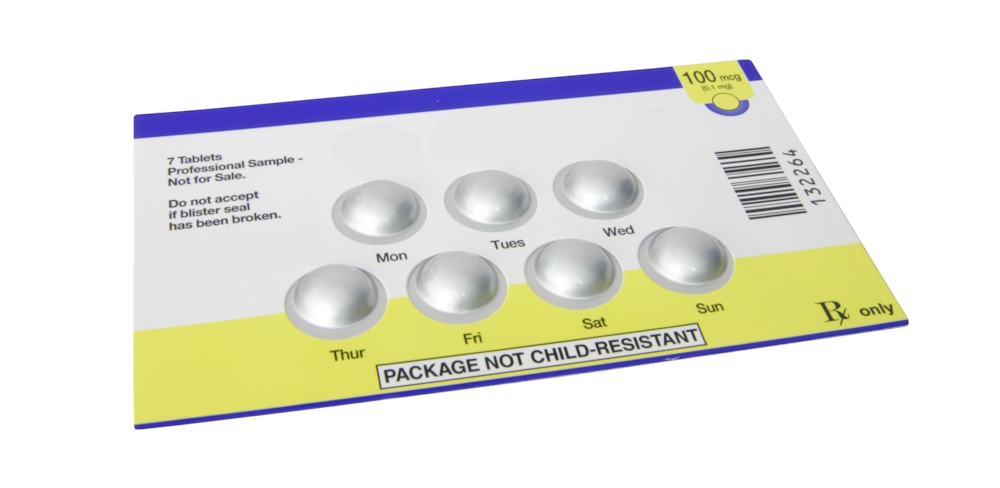
Given the extensive amount of heat sealing performed at contract packagers, it’s important to remember that machine maintenance plays a significant role in ensuring a uniform seal. Without proper protection, sticky sealing materials can collect on parts such as seal bars and jaws, and high heat and wear can affect sealing pressure and weaken seals. Not only can a weak seal allow contamination and poor product quality, this could create a long list of consequences that can include costly repairs, bottlenecks, missed deadlines, regulatory infractions and recalls, tarnished brand reputation and lost contracts. For these reasons, contract packagers in pharmaceutical, food and consumer industries turn to Magnaplate to resolve issues with their heat-sealing equipment. Here’s why:
How To Protect Aluminum During Heat Sealing
On pharmaceutical production lines, aluminum heat-sealing platens are used to produce carded blister packaging for medications. In other industries, heat sealing is used for diverse products like batteries, toys and pens, to name a few. Typically, a preformed blister is sealed to cardboard at up to 450°F and pressure up to 1,000 psi. The cardboard is usually printed and varnished.
Our Tufram® surface treatment is well-suited for contract packaging applications in the pharmaceutical and food industries because it does not transfer ink or varnish, provides excellent release properties and has the durability to hold up to the high heat and pressure of heat-sealing processes. In fact, Tufram features an operating temperature range of -360 to 850°F and complies with FDA and USDA codes.
Tufram combines a hard aluminum oxide ceramic with proprietary polymers to enhance the strength and durability of aluminum components like heat-sealing platens. When applied to aluminum alloys, Tufram exhibits a low coefficient of friction (COF) to protect against abrasive wear and galling that can otherwise cause stick-slip behavior or compromise your seals. It also dramatically increases surface hardness up to Rc 65. Other advantages include:
- Corrosion resistance.
- Thickness range of 0.0004 to 0.003 inch.
- Chemical and acid resistance.
- High dielectric strength.
- Won’t chip, peel or flake off.
Maintain Airtight Seals With Tufram
Whether you package medicine, food or toys, the reliability of your heat-sealing equipment will mean the difference between a hermetically sealed package and a compromised product. Tufram surface treatments are available with various benefits, and we can help recommend a coating type that best suits your specifications. With Tufram, your heat-sealing machinery will stand up to friction, wear and galling to deliver effective, air-tight seals and trouble-free performance. Be sure to talk with a Magnaplate technical expert to help determine the best Tufram coating for your aluminum heat-sealing surfaces.
For more information about Tufram surface treatments for aluminum components, visit our product page.