Coatings Technology Blog
When Protecting Magnesium Parts, Look Beyond Conventional Anodizing
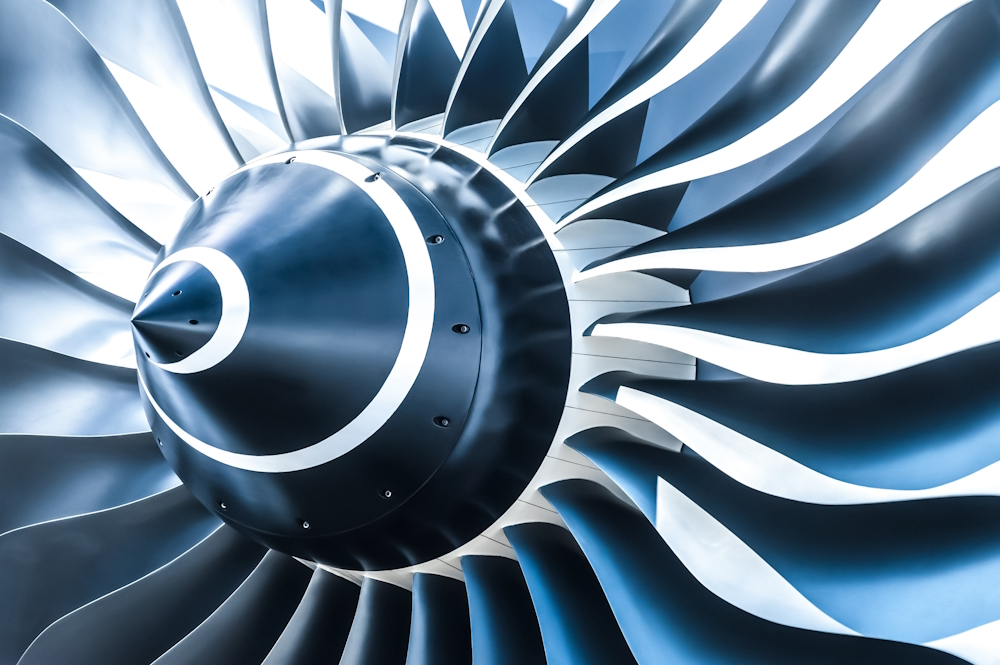
If you need to protect a magnesium part, you may automatically turn to an anodized coating to prevent corrosion. However, there may be times when an anodized coating won’t meet all your protective requirements. In these circumstances, not all coating providers are the same. When you need to protect your magnesium part against corrosion, chances are the part will need to resist other threats that a conventional HAE or plasma-type coating may not be equipped to handle. Here’s where a proprietary anodize-based surface treatment comes in.
A Proprietary Anodizing Process Goes Further
In a typical anodizing process, the part is submerged in an acidic electrolyte bath. Electric current is applied, producing a strong, corrosion-resistant finish. At Magnaplate, we take the anodic process even further. Our Magnadize® surface treatment is one of many anodic processes we engineer with dry lubricants, polymers and proprietary materials blended to enhance the performance of the metal’s surface.
Taken together, the Magnadize process not only provides corrosion resistance on magnesium alloys, it also protects against wear, outgassing and thermal extremes and minimizes friction, depending on the coating type selected.
Compared to conventional anodized magnesium coatings, Magnadize offers the following benefits:
- Corrosion resistance and lubricity. Magnadize coatings provide varying degrees of corrosion resistance and lubricity. For maximum results, discuss your part’s alloys and operating conditions with our technical team to determine the most effective dry lubricants and/or polymers for your application.
- Thick deposition. Thanks to additional dry lubricants and polymers after anodizing, Magnadize is typically applied at thicknesses ranging from 0.0002 to 0.0006 inch for optimal corrosion resistance.
- Wide temperature range. A wide temperature range of -100 to +550°F resists temperature extremes and vacuum conditions in space.
- Less friction and maintenance requirements. Magnadize exhibits a low coefficient of friction (COF), eliminating the need for lubricating greases and their inherent maintenance requirements.
- Availability. Throughout our 70-plus-year history of engineering surface treatments, we’ve coated thousands of parts for the space and aerospace industries that heavily rely on magnesium components.
- Additional features. Further features and specifications include:
- Meets Mil-M-45202 magnesium alloy treatment requirements.
- Dielectric strength.
- Select versions of Magnadize offer excellent release properties, and others exhibit exceptional COF.
Effective in Demanding Space and Industrial Applications
Magnadize is well-suited for demanding space and aerospace applications, as well as industrial applications like frames and housings, gearboxes, wheels, compressor components, air-operated tools and parts with weight or inertia constraints.
To find the best formulation for the job, our engineers can review your part’s requirements and suggest your best option. Let us know your magnesium alloy, part requirements, operating environment and other relevant application information so we can engineer a Magnadize surface treatment with optimal properties.
For more information about our Magnadize anodic surface treatment, please visit our product page.