Coatings Technology Blog
Carrying Forward a Legacy of Excellence in Aerospace
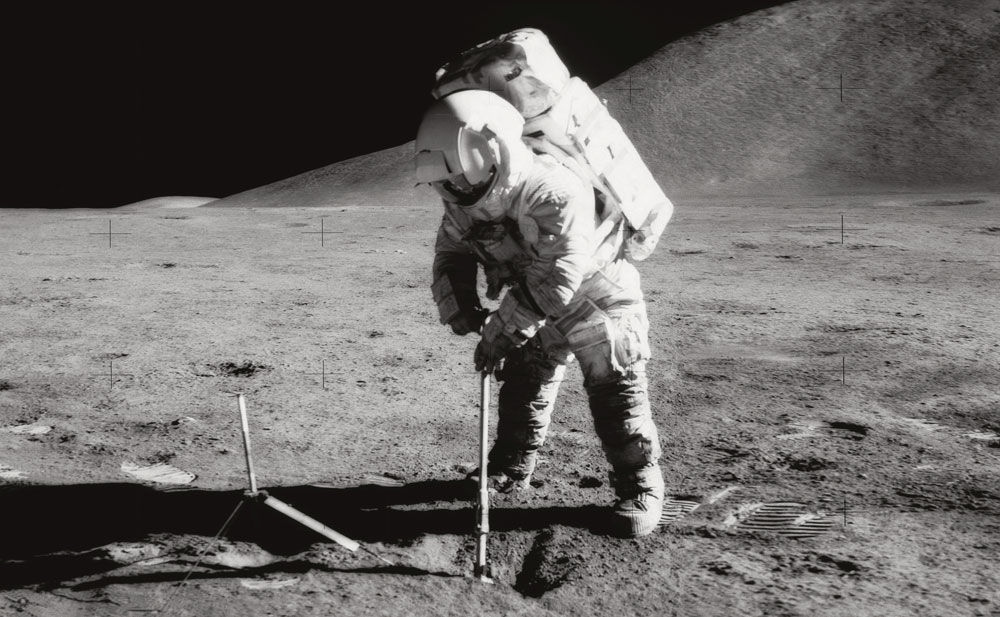
This year marks the 50th anniversary of the Apollo 11 mission to the moon. Magnaplate was part of the Apollo program's success from the beginning, both on the ground innovating surface coatings for space exploration and, later, on the moon protecting the drill tubes that sampled the moon's soil and rocks. Since our founding in 1952, Magnaplate has been creating synergistic coatings that withstand the extreme conditions that man and machine encounter in aerospace environments as evidenced by these space-exploration milestones:
- 1950s and 60s. Moved from non-destructive testing to a Tufram® surface enhancement facility that eventually supported NASA’s need for a coating on aluminum that did not outgas while resisting the harsh temperatures of outer space.
- 1969 — Apollo 11. Magnaplate’s Canadize® treatment is used on the inside and outside of the titanium core-sample drill tubes to prevent galling and contamination of the moon rock and soil samples.
- 1970. Synergistic coatings protect the fuel-mixing control valves on Apollo 13’s LEM Ascent Engine.
- 1980s. NASA gears up its space shuttle program, requiring surface enhancements that provided extremely hard, dry-lubricated surfaces on hundreds of aluminum, titanium and steel parts, tools and other equipment.
- 2004. Magnaplate’s coatings play a role in the Mars Rover’s descent rate limiter.
- 2012. Magnaplate coats parts for commercial spacecraft and NASA’s Curiosity Mars rover.
- 2019. Magnaplate celebrates 67 years of serving the aerospace industry.
Today, Magnaplate provides many commercial airframe and aerospace companies, as well as commercial spacecraft, airline and military companies with REACH-compliant synergistic coatings that ensure parts withstand extreme conditions. Here’s how Magnaplate synergistic coatings — featuring permanent dry lubrication, a low coefficient of friction and good thermal tolerance — protect against common environmental threats in the aerospace sector:
- Friction. Synergistic coatings protect against abrasion and galling, a form of wear caused by adhesion between sliding metal surfaces. Products include Canadize® for titanium alloys and Magnadize® for magnesium alloys, Tufram® and Magnaplate HCR® for aluminum alloys and Nedox® for ferrous and non-ferrous base metals. These products offer a dry lubricated permanent solution that reduces maintenance and increases part lifetimes.
- Corrosion. Magnaplate’s coatings for aluminum can help aerospace and aircraft manufacturers replace heavy metals such as steel in many aerospace applications. Tufram® can elevate the surface hardness of aluminum to levels comparable to case-hardened steel while resisting corrosion, and HCR® coatings offer aluminum salt spray exposure performance 44-times the MIL-SPEC requirement.
- Extreme temperatures. Plasmadize® coatings feature an operating temperature range of -200 to 1,300°F, provide easy mold and die release at high temperatures and are a perfect fit for composite tooling and autoclaves.
Synergistic Coatings Are up to Present and Future Aerospace Challenges
The metal components used in space systems and other aerospace applications must be able to withstand corrosion, friction, thermal and other threats. Since the very first NASA space missions, synergistic coatings have been up to the challenge, offering corrosion and wear resistance, permanent dry lubrication, protection against outgassing, thermal tolerance and REACH-compliant protection for steel, aluminum, titanium and other super alloy components. As Magnaplate celebrates the success of Apollo 11 along with the rest of the world, we eagerly look forward to contributing to future missions that expand humankind’s presence in the final frontier.
For more information about how Magnaplate synergistic coatings meet aerospace challenges, Download The White Paper.